The European MOSES research project, aims to significantly enhance the European Short Sea Shipping container supply chain by implementing a constellation of innovations including innovative vessels and the optimization of logistics operations.
TNO’s work within MOSES focuses on developing and demonstrating a Robotic Container Handling System that, when mounted on an electric and unmanned feeder vessel, enables unmanned containers logistics to local ports without loading and unloading capacity.
Normally, a crane operator controls the crane based on his/her eye-hand coordination, e.g. knowing which container to pick-up, he/she looks for the position of the container, estimates the distance between spreader and container, reduces speed if needed, locks, etc. Furthermore, the safety of the operation is guaranteed with a relatively high degree of oversight from other people as well as the creation of a secured and sealed-off area. The RCHS research challenge is to bridge the large gap between the current way of working and the envisioned concept where the RCHS can perform all these tasks on its own, i.e. autonomously.
The RCHS is approached as a systems-of-systems. In fact, the RCHS consists of five major components, each consisting of multiple subcomponents
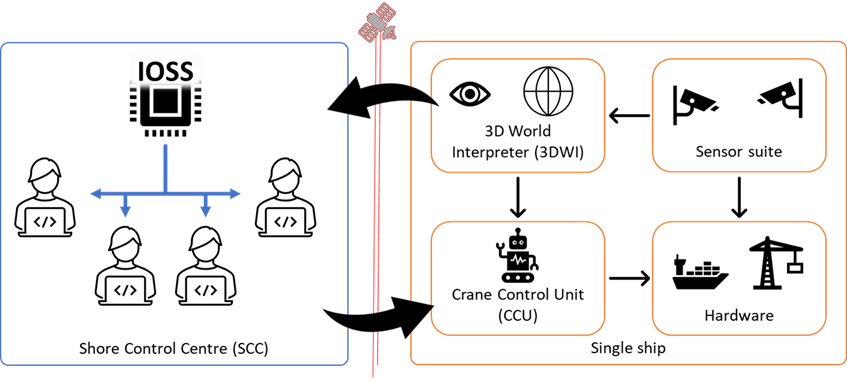
- The crane, spreader, and automatic swivel control system.
- The Crane Control Unit (CCU), responsible for both the control and high-level decision-making needed to load and unload containers safely in a public area at a small port. The control functionality of CCU is responsible to drive the crane and all of its sub-components. The decision-making function is responsible to decide which container to load or unload when and where.
- The 3D World Interpreter (3DWI), is responsible for the perception (detection) of elements in the environment, comprehension of what they mean (identification) and how they relate. This SA is required by the CCU for controlling the crane and high-level decision-making. Likewise, it provides the local information needed both for operator SA as for the functions the operators support. Combined, the CCU and the 3DWI is the core of a self-sufficient autonomously operating crane system.
- Sensor suite, a combination of (stereo) cameras and lidars to provide the 3DWI with images of the operational area.
- The Intelligent Operator Support System (IOSS) is responsible for safely managing a large amount of autonomous container handling operations occurring in parallel and their supervision from a remote shore control centre. This AI-based computer system ensures that every ongoing operation is performed effectively and safely. It does so by providing support to enable only a few operators to supervise many operations. Examples are the allocation of operations, SA support, risk assessment, control suggestions and more.
Remote supervisory operator control consists of a front-end interface based on a progressive disclosure interaction design. It is an interaction design pattern that provides a user with increasingly more and detailed interactions about a topic. The pattern entails the idea that interactions (or control signals) should start simple, and progressively become more complex and intricate based on previous interactions and the situation. The reason to do so is to prevent overload, reduce the risk of human-error, and prevent micro-management. For IOSS a three-layer interface has been developed that progressively discloses more information about the operations an operator supervises and enables increasingly more complex and involved control actions. These three layers are; 1) a global view providing an overview of the entire fleet an operator is responsible of, 2) a localized view providing an overview of the status of a single ship, and 3) a situational view providing an entirely immersive view using virtual reality on a single situational perspective of a ship.
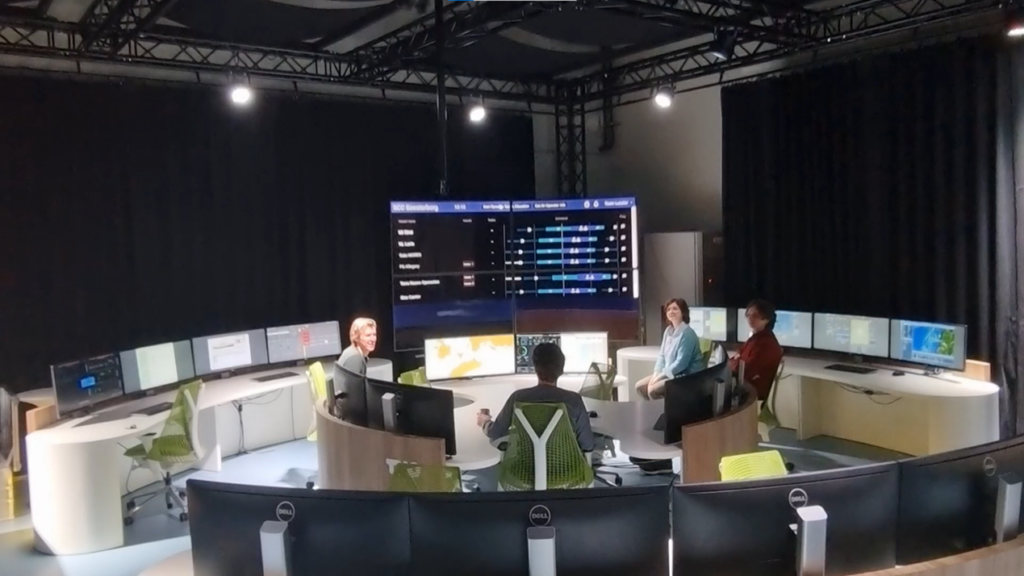
Acknowledgement
Within the RCHS research and development TNO closely collaborate with MacGregor Finland Oy, the company that provides the physical crane system and crane control software.
This research has been conducted as part of MOSES project, which has received funding from the European Union’s Horizon 2020 Research and Innovation Program under Grant agreement No. 861678.